How do you encourage innovation and ensure that you’re consistently on the right side of the curve? This is an integral part of the culture of any successful engineering business – here's we approach it.
This article was guest written by IGS’ Head of Hardware, Steve Waldron. Steve and his team help ensure our Growth Towers deliver the best possible customer experience and that they are primed for perfect plant cultivation.
As Head of Hardware at Intelligent Growth Solutions (IGS), a large part of my role is focused on ensuring the right conditions are in place for continuous innovation. The Oxford Dictionary defines innovation as ‘a new way of doing something’. Stripping it back, you might say that – relatively speaking – vertical farming is just that. But to truly succeed in any fledgling industry, it’s vital to ensure that your product remains not only up to speed, but goes above and beyond user requirements to provide the best possible customer experience.
Every decision needs to have the concept of innovation at its heart. User-centred design is crucial – not only for ease of use but also in terms of durability (particularly when the product could be used to produce food on a scale never seen before). Over the years, we’ve focused on putting fundamentals in place across our engineering teams to make this a reality.
Changing the culture
I’m a firm believer in diversity of input. Our company is built from fused disciplines – the crop science arm of IGS compliments the data science one, while the hardware and software engineering teams dovetail nicely with both. This diversity of input helps catch any issues before they grow into larger problems, ensuring that every aspect is looked at from all angles.
Once we’ve ideated anything product related, we have policy in place that ensures nothing gets to a customer site without rigorous testing. We’ve got to be quite innovative about how we do this. It can hard to test how one change might affect operations at scale, so to ensure we’re considering potential challenges from all angles, we bring in discipline experts from across IGS. This is particularly beneficial when working with those who have experience working directly on customer sites, or who have specific agronomy experience.
Looking from the outside in
There’s only so much that can happen stuck behind a desk, so we encourage teams to attend conferences and trade shows wherever possible, as well as spending time on customer sites with our deployment teams. This helps build a clear picture of how the hardware comes together in practice, alongside a consideration of all the other practicalities which go into making it a fully functional product.
It’s also fruitful to bring in external expertise. An example of this would be our work with the Fraunhofer Institute to consult with experts in optical design. They’ve supported us in developing metrics and validated the uniformity of light across our Growth Trays. We can’t be experts in everything, therefore it's important to recognise where it helps to bring in external expertise, continuously improving and working towards creating the best possible product for our customers.
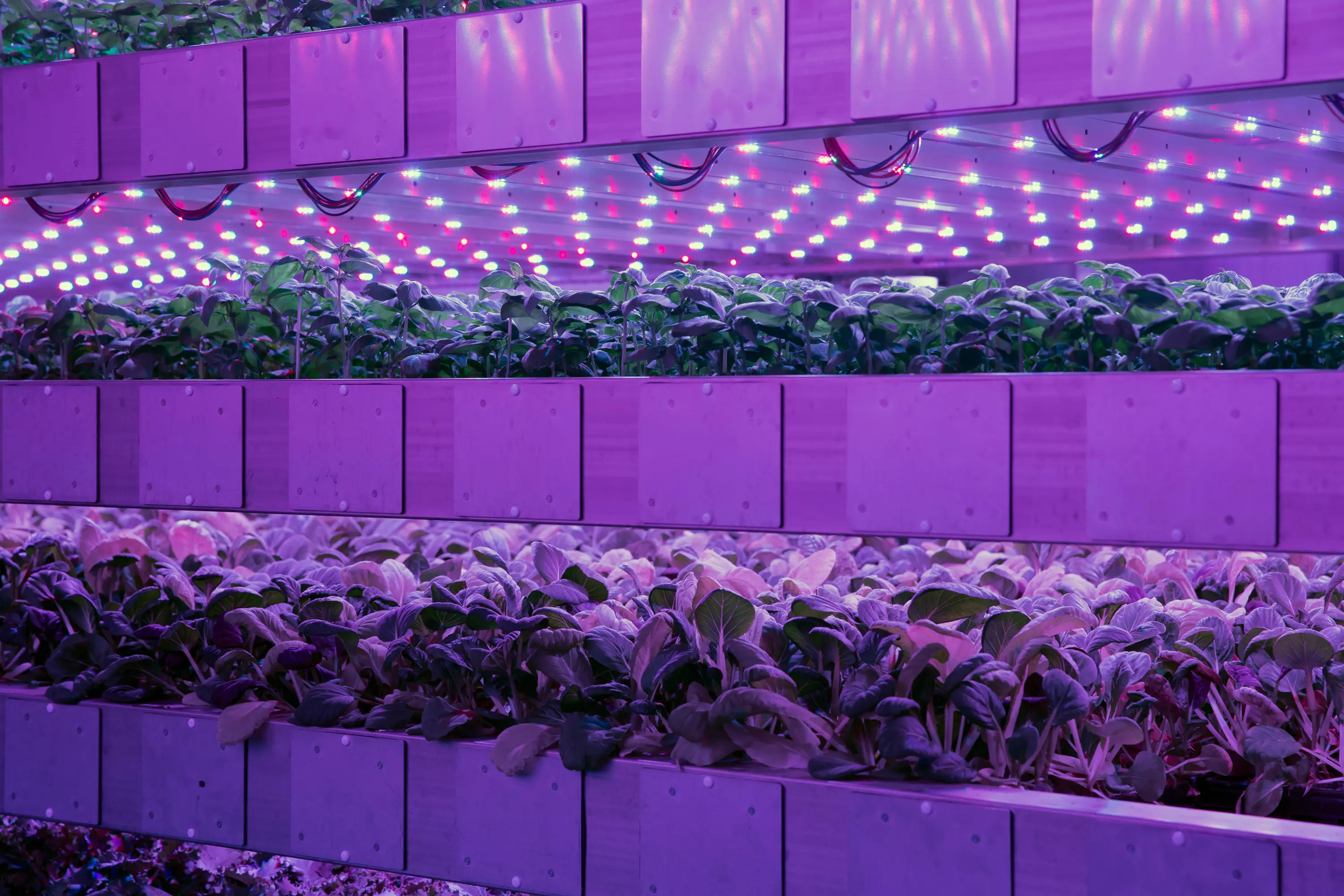
Breathing new life into our product – increasing airflow
One concrete example of these practices in action would be the recent changes we’ve made to increase airflow in our towers. As well as customer feedback, we rely heavily on internal observations about how IGS technology works in practice. We know that having more airflow can allow us to have more influence over crop behaviour, for example, so we tasked our engineers with looking at this as part of one of our regular one-day hackathons in April 2024. By taking time away from their usual daily tasks and working with colleagues outside their day-to-day teams, they can generate ‘outside-of-the-box' thinking. Harnessing our knowledge of how air flows through the tubing, a team of our engineers was able to develop a concept which minimises noise.
A second team spent the time working on a solution to allow for at least 25% more airflow in our towers. We’ve since proved this through rigorous testing, before retrofitting the change to customer sites to allow them to get the most from our technology. This was something we wanted to roll out at speed, so the product change came around quite quickly after the initial hackathon. It wasn't necessarily a change that came from the top down – it's a result of talented people getting in a room together and thrashing out a solid solution.
Through the hackathon, we also developed a pressure testing rig. As soon as we could trust the results from that, we used it as a proxy for what we could expect on customer sites.
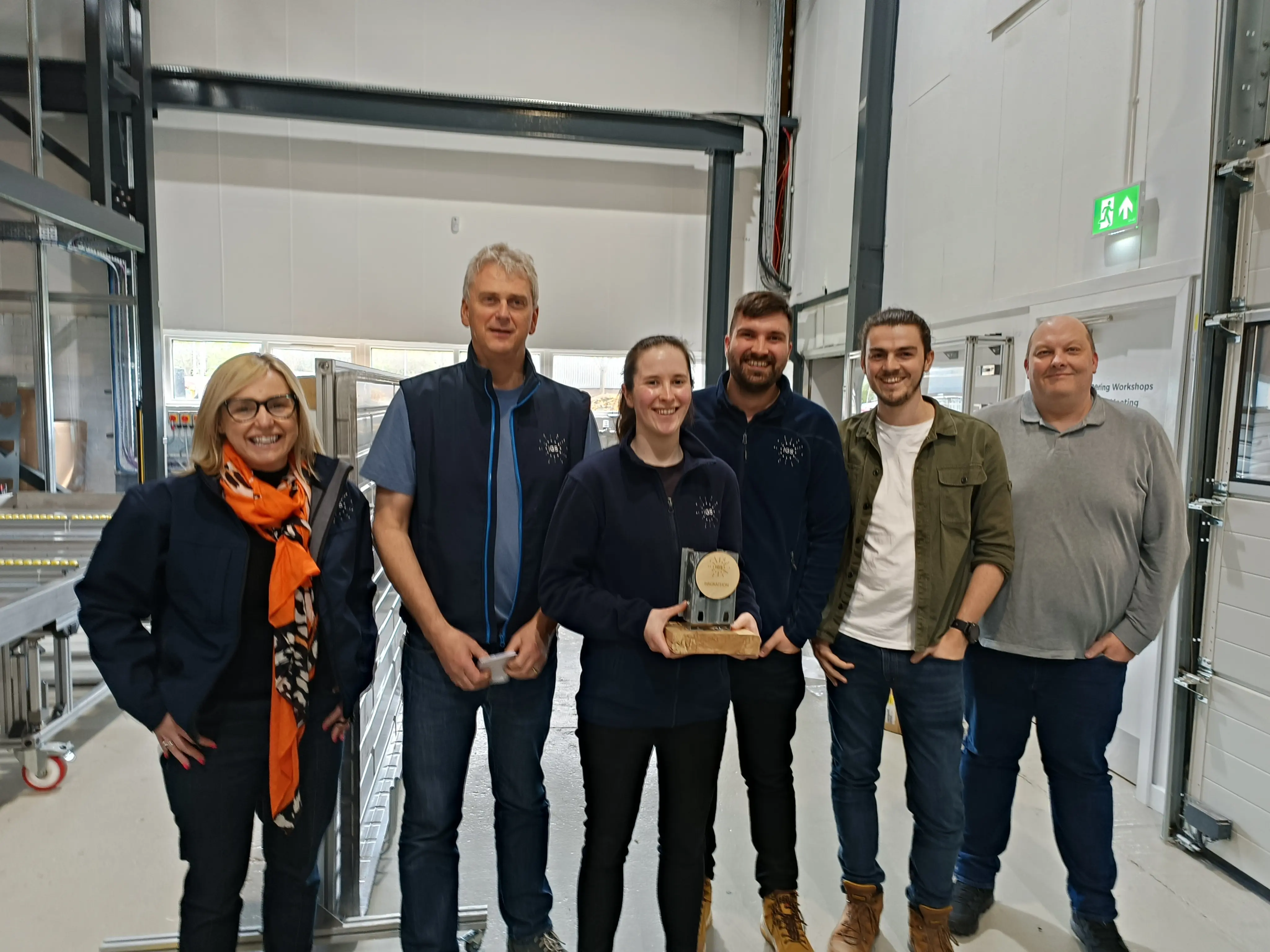
The value of experimentation
Our approach to design is complex, but at its core involves looking at results from a different angle and always aiming to learn something new. The way in which we change the hardware can have a knock-on impact on how the plants grow, so consideration of plants plays a big role in the performance of the system and how we calibrate it. We have to be mindful of the interactions with what’s growing in the environment and how plants might interact with it – this influences the overall outcome.
To ensure we’re covering all bases, we always use a cross-disciplinary approach. In various projects, this has involved everyone from hardware engineers and software engineers through to crop and data scientists. We’ve all got one key goal – ensuring the best possible product – so it pays to collaborate and analyse all the different variables and how they interact with one another.
Finding the perfect lining
A lot of success in engineering comes from using the right manufacturing materials to suit the scale of the project at hand, in line with the budget. We were looking into how our product could change to be used as part of a GigaFarm in Dubai. The scale of a GigaFarm opened up a whole new range of manufacturing possibilities which we’d never been able to utilise until now, using new materials and fine-tuning different aspects of our Growth Towers.
We’d initially looked at plastic liners, but this proved difficult as the material spec we require is demanding – it's also got to be both fire safe and food safe. The size of the liner is also a challenge. These liners are enormous! We’re talking about something which is four metres long and one and a half metres wide, so this stretches the limits of what can physically be made in a mechanical press.
As luck would have it (as is often the case in engineering!) we were in conversation with a manufacturer in Europe that would allow us to manufacture metal liners using a press tool that could handle the scale of the task at hand. This came at a cost, however, so we needed to de-risk and test every possible outcome. We did this through a specialist agency, ensuring no stone was left unturned and analysing the process thoroughly. They had very advanced computational fluid dynamics, as well as mold flow analysis (MFA), which they could use to predict outcomes to change before production started.
The whole process took around nine months to get a usable liner, and then a year to really garner first impressions. We trialled a few different iterations, but by testing thoroughly and opening our minds to how we could do things differently to before, we were able to come to a decisive conclusion. The end result is a liner which is fireproof, doesn’t contain mixed plastics, and is on the whole far more environmentally friendly than a solely plastic version. By looking at the supply chain and how we could get the most from it, we were able to innovate and solve a problem before it ever materialised.
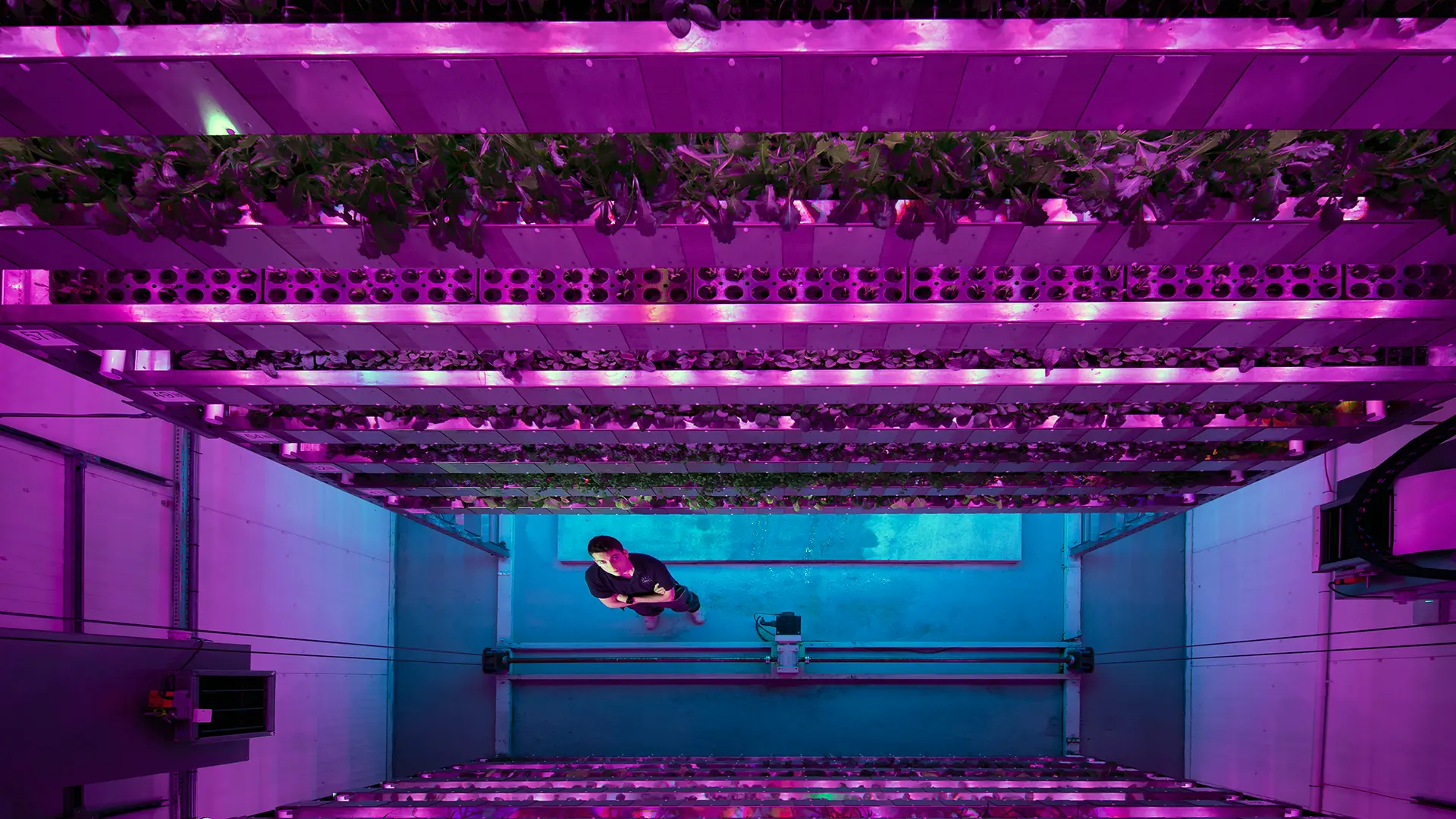
What lies ahead
The future is exciting for vertical farming. After a few challenging years in the industry, we’re starting to see what lies ahead and how the technology can be applied at scale. Innovation is at the heart of this – if we can adopt practices which make it not only likely, but inevitable, we’ll be ready to face challenges on the road to scalability and yields greater than we’ve ever previously imagined.
Want to learn more about how our technology can continue to iterate and benefit your operations? Get in touch.